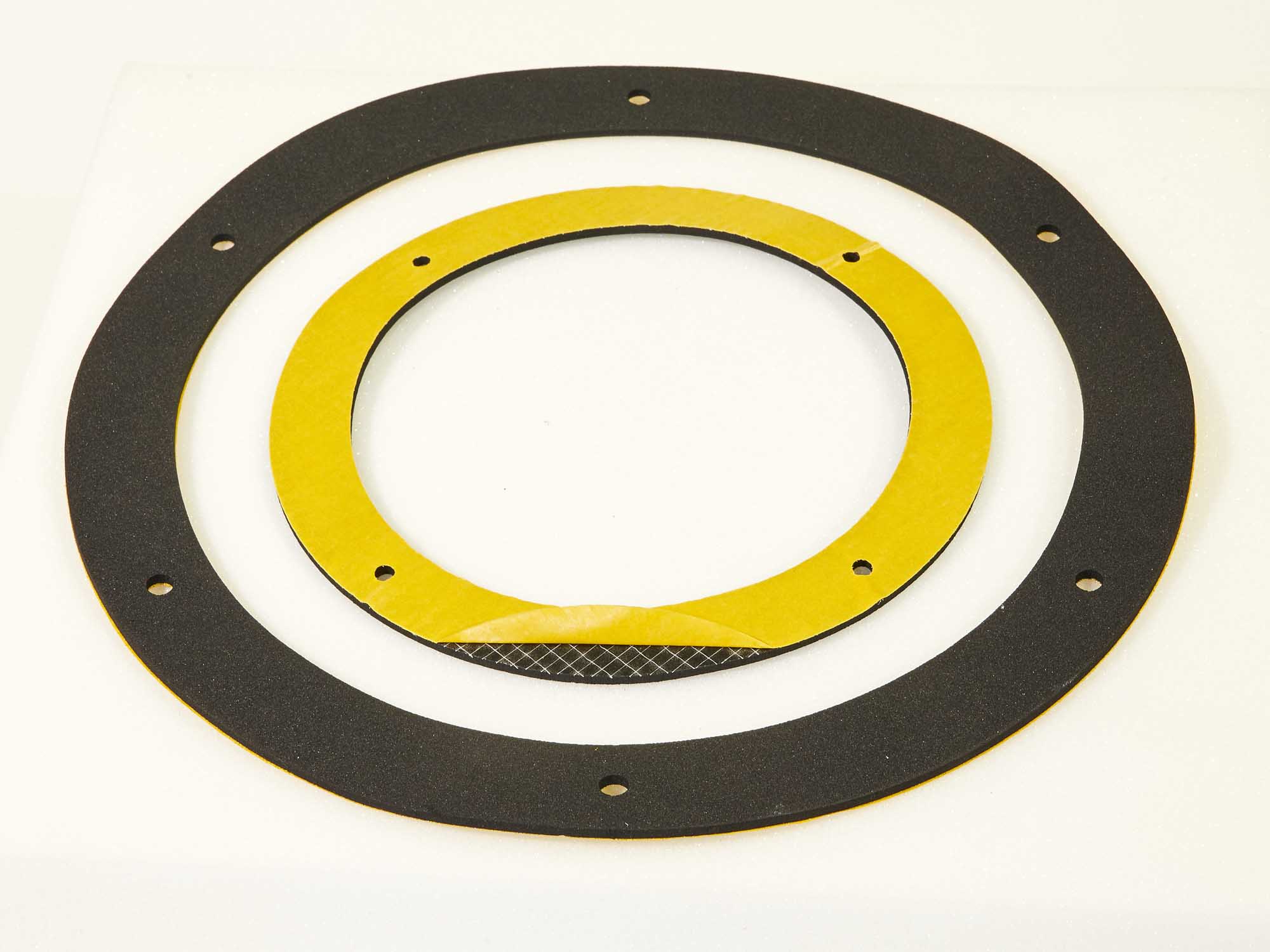
By their nature, closed cell products are suitable for use as seals and gaskets.
Because this is an extremely wide category, which includes expanded polyethylenes (often in compounds with other materials) and all expanded elastomers, the characteristics can be very varied; from temperature resistance, fire resistance, low oil absorption and, of course, greater or lesser hardness, elongation and permanent deformation.
Expanded polyurethanes can also be used in this field; if you are looking for a soft product adaptable to different thicknesses, we have special formulations that form an impenetrable barrier to air and water when compressed to half of their thickness.
Other polyurethanes are used as seals in goggles and ski goggles and come into direct contact with the skin.
Let’s take a closer look at some of the main characteristics of these products:
Expanded polyethylene: generally low specific weight products are used (even if we are able to reach over 200 kg/m3) when there are no elevated needs from the point of view of contact with chemical products and, above all, temperature; this is a rather low-priced product.
Expanded EPDM: it can be pure or, more often, mixed with other products such as PE, EVA or others; the working temperatures can reach 120 – 130 °C when pure, while hardness and density can vary greatly, from 60 to over 400 kg/m3; this is one of the most used products due to the good quality/price ratio.
CR neoprene: very similar in appearance to EPDM, it generally has slightly better ozone and fire resistance qualities and good resistance against tearing and elongation up to the breaking point, so it is more suitable for heavy duty use, where it might be more stressed.
NBR and SBR are mainly used when the seal can come into contact with mineral oils, against which these materials have excellent resistance and low or no absorption.
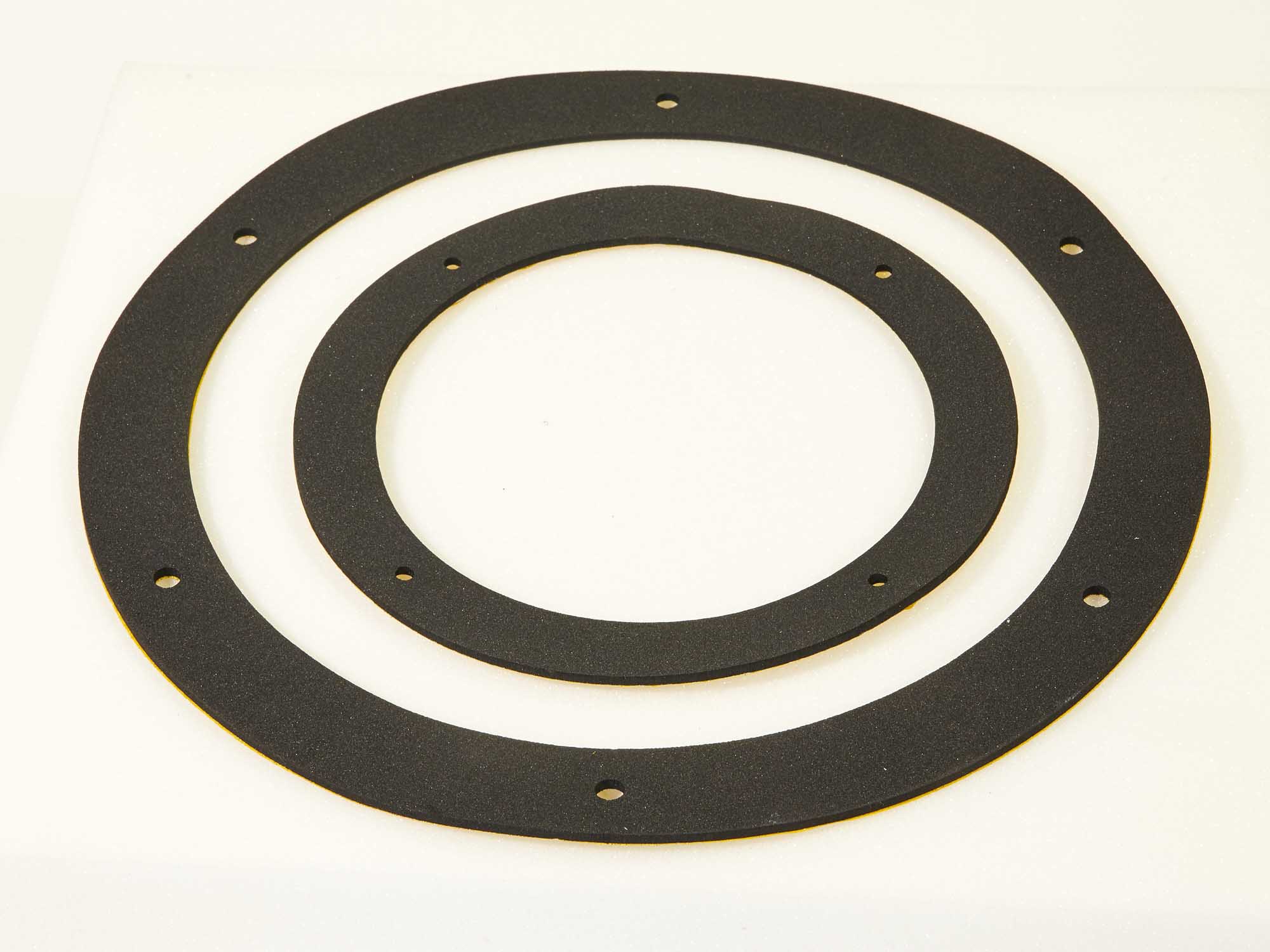